1000级药厂外包gmp净化车间净化工程
浏览次数:627次
- 产品规格:
- 发货地:广东省深圳市宝安区
关键词
十万级gmp药厂无菌车间净化工程
详细说明
除尘率99.99%
净化级别百级千级万级十万级等
加工定制是
吹淋方式空气吹淋
适用面积20平方米
中净环球净化可提供GMP车间、药厂车间、洁净工程、无尘车间、实验室的咨询、规划、设计、施工、安装、改造等配套服务,技术、经验丰富、价格实惠。离心
离心工艺验证时应主要关注离心、洗涤工艺的效能确认,对离心设备本身的离心、洗涤效能的确认可能在性能确认时已使用模拟物料进行过确认。在工艺验证阶段应该针对商业化生产规模的产品生产对离心和洗涤效能的重复性和稳定性进行确认。
评价离心效能的指标应考虑:
①滤饼湿含量 目前离心设备配置在线滤饼取样装置日益增多,但需注意,由于湿分往往是易挥发的**溶媒,因此取样和取样后的样品处理应保证样品中的湿分含量不发生变化,即样品与实际离心结界后中间产品湿分的一致性。
②离心时间 即从结晶悬浮液进料到甩干的时间。
③母液澄明度 应考虑由于结晶料液温度往往低于室温,离心后母液管道和储存设备均未配置保温,当母液温度升高后可能会造成透过离心过滤介质的晶体溶解。
评价洗涤效能方式可考虑:
①滤饼洗涤前后的杂质水平或**残留水平(当采用其他溶媒洗涤时,例如水洗),洗涤后的产品杂质水平应该符合产品质量标准的要求;
②洗液pH 主要适用于当洗涤的主要目的是除去滤饼中的酸或碱时。
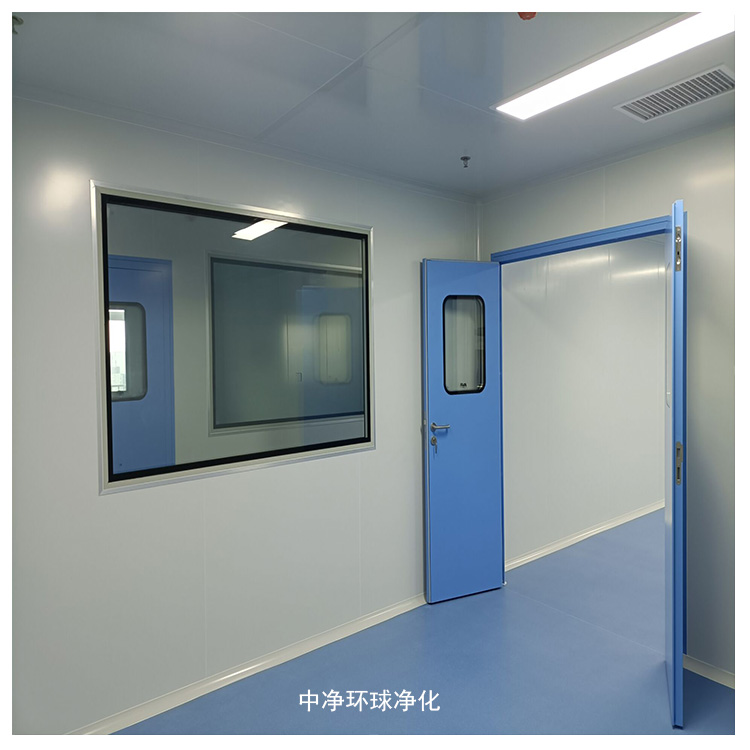
1.原料药工艺流程概述
原料药的生产即通过化学合成、培养或发酵提取、**资源回收,或通过以上工艺的结合而得到目标成分,按照制备工艺分为化学合成原料药、发酵类原料约和动植物提取类原料药,按照产品特性分为无菌原料药和非无菌原料药。
a.化学合成原料药的生产工艺
化学合成是原料药生产的主要方式之一,通常是起始物料与其他化合物通过若干步骤的化学反应得到特定化学结构的目标产物,如缩合、取代、酰化、氧化还原等;然后再经过一步或几步的精制,如脱色、过滤、重结晶、干燥等,得到终的原料药产品。
化学合成类原料药中间体和粗品在无洁净级别生产区生产,而终成品的精制、干燥和包装工序通常在D级洁净区进行。
b.发酵类原料药生产工艺
发酵也是原料药生产工艺的主要方式之一,尤其是抗生素类原料约,如青类、类等,通常是通过发酵和化学合成的半合成方式得到的。此类生严工艺先通过生物发酵得到目标化合物的主要结构,例如青的β-内酰胺结构,然后再进行结构修饰,得到终目标化合物,再经过精制如重结晶得到终原料药。发酵过程一般需要经过菌种接种、发酵培养、过滤、反应、精制等步骤。
c. 动植物提取类原料药生产工艺
自然界是**的化合物宝库,动物或植物通过新陈代谢,产生了许多仅靠目前的合成手段无法实现却对疾病有重大意义的化合物,因此动植物提取是获取目标化合物的重要方式,也是生产原料药的主要方式之一。如疟疾的,从动物内脏中提取得到的用于心血管疾病的肝素等。
近年来,通过从动植物组织中提取得到生产原料药的中间体,再通过一定的化学合成和结构优化,终得到目标化合物,这样不仅能大幅提高其疗放,还能进一步地减少其毒。例如药物喜树碱,通过进一步的结构修饰,得到选择性好,毒小的盐酸伊立替康、拓扑替康等药物。
一般来说,动植物提取类原料药的生产工艺分为4个部分,即原材料的前处理、提取、结构修饰和精制。
d. 无菌原料药生产工艺
按产品的微生物水平和目标剂刑,原料药分为非无菌原料药和无菌原料药。无菌原料药又分为终灭菌的无菌原料药和非终灭菌的无菌原料药,但由于原料药大多对高温高热、高湿高压、辐射等敏感,采用终灭菌的无菌原料药很少。目前非终灭菌的无菌原料药通常是将产品一步精制成盐或与除菌工艺相结合,采用预过滤加两级0.22μm 的除菌过滤实现终产品无菌的。经过除菌过滤后的药液通常采用结晶、冷冻或喷雾干燥的方式得到终的无菌原料药产品。
无菌原料药前段生产工艺根据活性成分获取来源,在上述a、b、c分别进行了介绍,以下将从粗品处理开始介绍无菌原料药生产工艺。在传统的无菌原料药生产中,粗品的溶解、脱色在C级洁净区进行,除菌过滤、结晶、离心/过滤、干燥粉碎、混合、分装是在B级洁净区加A级层流环境下进行。目前,无菌原料药越来越多地采用密闭系统装备,降低了无菌操作过程污染风险的同时降低了生产过程对外界环境洁净级别的要求。
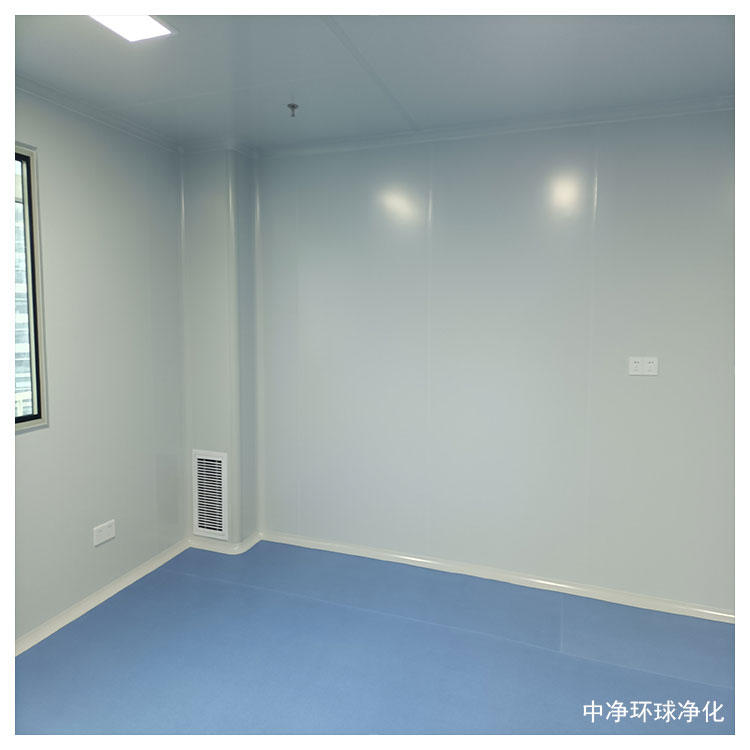
口服固体制剂工艺流程概述二
4.干燥
湿颗粒制好后应立即干燥,避免结块和受压变形,干燥温度和时间根据API 及湿颗粒性质而定。以沸腾干燥为例,通过使热空气自下而上通过松散的物料层形成沸腾床而进行干燥,它基于颗粒在空气中的悬浮和移动,并由此产生了一个从空气到颗粒有效的热传递以及液态到气态的有效转化。操作中随时注意流化室温度,颗粒流动情况,应不断检查有无结料现象。通过测定含水量进行控制,水分过高,压片时易发生黏冲,太低易发生裂片现象。换品种时洗净或换滤袋。
5.整粒和总混
对于干燥后的颗粒需要进行适当的过筛整粒,使彼此粘连结块的颗粒散开,得到大小均匀一致的颗粒,整粒机的落料漏斗可选择安装金属探测器或采取其他有效的手段和方法,除去意外进入颗粒中的金属屑。
整粒结束后根据工艺加人润滑剂、崩解剂等外加物料进行总混。混合机内的装量一般不宜**过该机总容积的2/3。
6.压片
压片机简单描述为将颗粒或粉状物料置于模孔内由冲头压制成片剂的机器。机型可分为单冲式压机、花蓝式压片机、旋转式压片机、亚高速旋转式压片机、全自动高速压片机以及旋转式包芯压片机。目前多采用高速旋转式压片机。通过上下两个固定冲头把相等体积颗粒压缩在一个个固定模孔中压缩成型,可以做成不同的大小和形状。这种高速旋转压片机具有强迫供科机构,机器由PLC控制,有自动调节压力、控制片重、剔除废片、打印数据、显示故障停机等功能,除能控制片重差异在一定的范围内以外,对缺角、松裂片等质量问题能自动鉴别并能剔除废片。
压片机的加料宜采用密闭加料装置,减少粉尘飞扬。压片机应有吸尘装置,除去粉尘。
7. 包衣
片剂包衣是为了防止药片芯片氧化变质,又可隐盖药片芯片的不适之味,还可缓和在人中的溶解过程。包衣的基本类型包括糖包衣、薄膜包衣(胃溶型、肠溶型和水不溶型)和压制包衣等,包糖衣和包薄膜衣在实际生产中为常用。
糖包衣的一般流程为:被片芯放入包衣滚筒内,先对锅内芯片分次喷糖浆,再通过锅体时针旋转,使糖衣片在锅内翻滚、摩擦、研磨,使糖衣均匀。同时向锅内通入热风,去药片糖衣表层水分,获得包裹均匀、光滑的糖衣片。
薄膜包衣的一般流程为,将片芯放入包衣滚筒内,不停地做复杂的轨迹运动,运动过程中,按工艺流程和参数自动喷洒包衣液,同时供给冷热风。使包衣层得到快速、均匀的干,形成坚固光滑的薄膜衣层。
通常包衣液根据用途不同,采用不同的辅料和适宜的溶剂配制而成。
8.包装
包装分内包装和外包装,生产过程多采用铝塑盒装或瓶装盒装两种包装形式。由包材供单元供应包材,下料单元提供待包装半成品经过成型单元或灌装机将其密封成型,人工或自动设备检查缺损或密封不严等情况,之后进行机械装盒,自动装箱打包。
以上仅是根据现有片剂生产工艺为常见的湿法制粒、压片、包衣和包装工艺进行了工步骤的简单介绍。田于片剂的制剂工艺繁多且复杂,所以未作一一赘述。
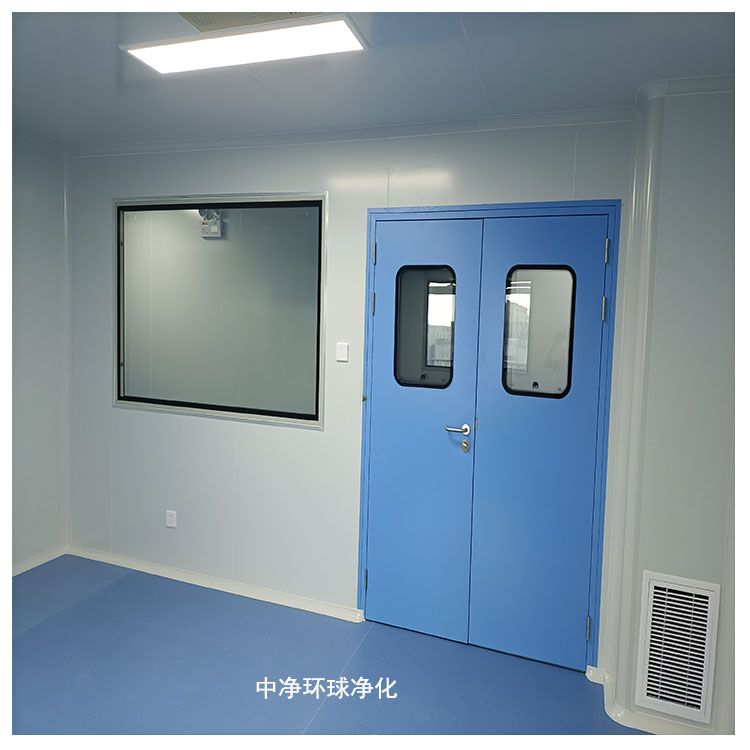
原料药工艺风险评估
ICH Q9和 PDA技术报告44号中定义了若干风险评估的万法,本文讲述如何使用危害分析和关键控制点(HACCP)进行原料药工艺风险评估的基本流程。
危害分析和关键控制点是确保产品质量可靠性及性系统的、前瞻的及预防性的工具。它是一个结构性的方法,其通过采用技术和科学原则去分析、评价、预防和控制由于产品的设计、开发、生产和使用带来的风险或不利结果及危险因素。通常情况下,通过 HACCP确定出生产工艺中所有的潜在危险和关键控制点,并记录在文件中,保证具有适宜的控制,并以的方式生产该产品。这种评估为生产工艺关键控制点的制定提供了支持。进行风险评估之前应该确定产品的关键质量属性和关键工艺参数、生产批量和生产组织的方式,并且应附有关键工艺参数的产品工艺规程。
以某原料药酸化结晶工序的风险评估举例,此工序步骤可能包括的关键工艺参数有配料比、料液浓度、温度、pH、压力、搅拌速度、反应时间、滴加速度、加热或冷却速率、搅拌转速或其效果(对多相体系重要)等。
以上述酸化结晶工序为例,讲行工艺风险评估时需要执行以下步骤:
①明确与该工序相关的产品关键质量属性和关键工艺参数并进行风险的识别。例如,盐酸的浓度不符合要求;加酸过量,料液pH**出2.2~3.0的范围;养晶时间不符合工艺要求;温度**出控制范围等;
②进行危害分析,分析各个危害发生的可能性及严重性,然后确定该控制点的关键性;
③对关键控制点采取相应的措施,如建立警戒限,例如养晶温度严格控制在10℃士1.5℃;建立关键控制点的监测程序,例如采取双人复核关键控制点的操作、增加中控检验,例如加酸完毕后搅拌10min后再取样复核等;
④确定适当的纠正措施,例如pH大于3.0,可再加酸直至符合标准;
⑤制定或修改SOP,在SOP中定义关键控制点的控制措施,记录并保存。
中净环球净化承接各类行业大小室内净化工程,净化工程设计施工,净化设备安装等配套服务
专注无尘洁净室工程,深度净化,为您提供可靠放心的产品。
ccg009.cn.b2b168.com/m/